The Crunchbase “Female Founder Series,” comprises stories, Q&As, and thought-leadership pieces from glass-ceiling-smashers who overcame the odds and are now leading successful companies.
Maria Telleria is the co-founder and CTO of Canvas, a construction robotics startup that is building the future in bold new ways. She’s passionate about creating machines that make construction safer and open up more opportunities for skilled workers.
During her childhood in Mexico, Telleria was always “tinkering,” often helping family members fix things that were broken. When she moved to the United States at 14, she joined the robotics team at her high school—sparking an interest in mechanical engineering. This started her on a path that would take her to MIT, where she earned her undergraduate degree and later her Ph.D.
Now, Telleria is bringing innovation and automation to the world of construction by building robots for the industry’s workers. In this Q&A, she shares the story of her career from robotics researcher to startup co-founder, how Canvas is shaking up the construction industry, and her advice for female entrepreneurs and young girls interested in robotics.
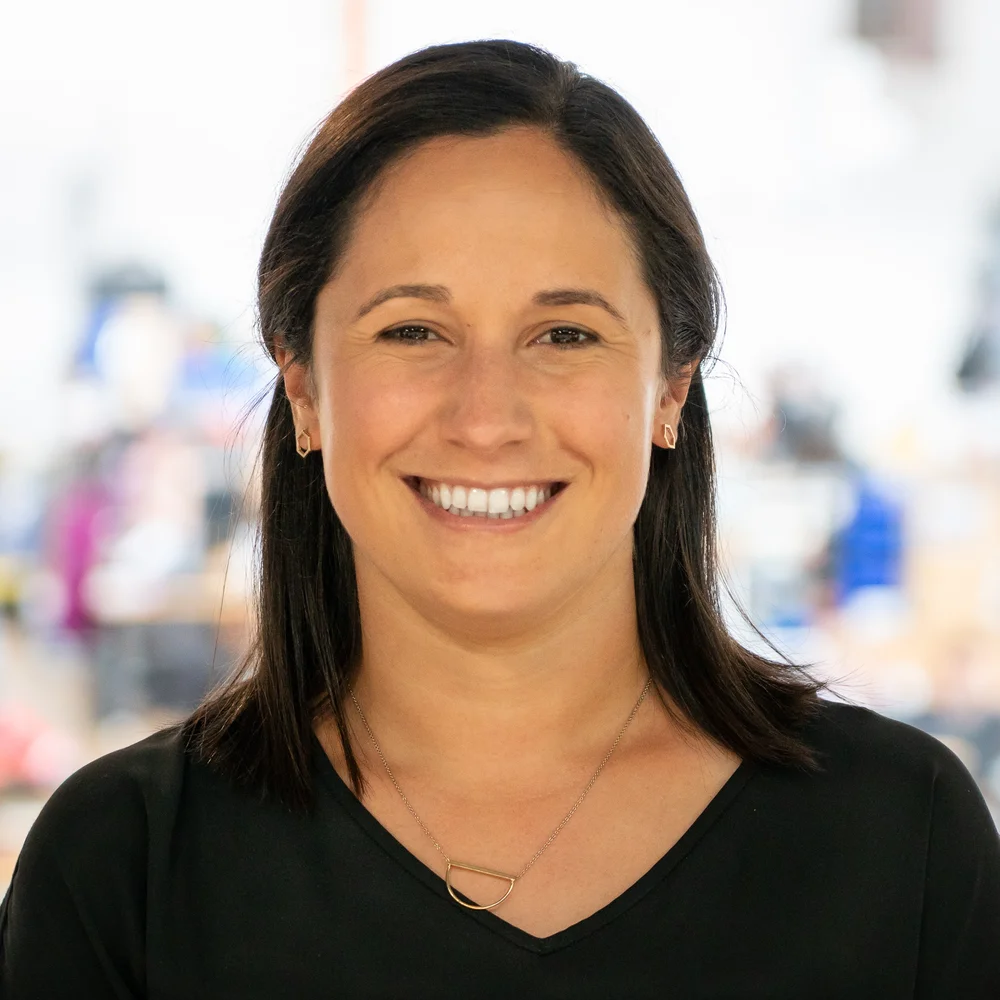
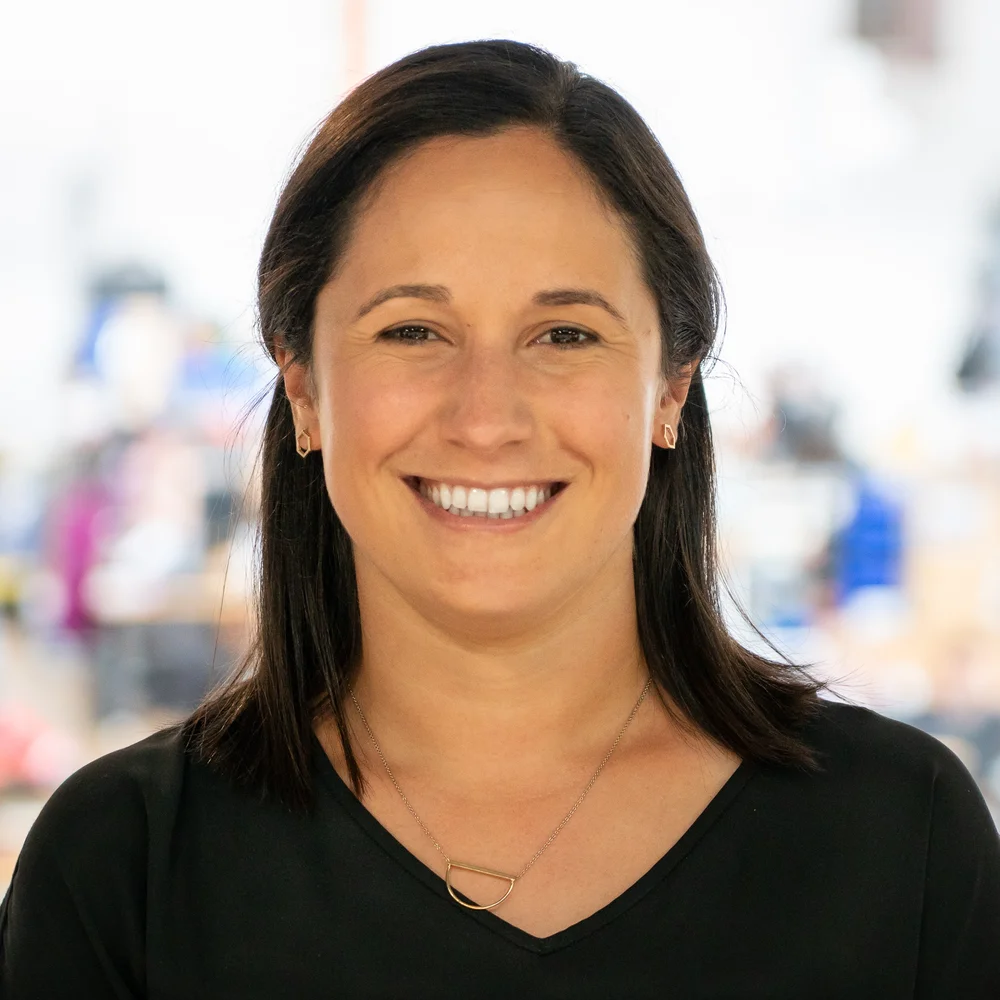
Q: Why did you pursue the fields of robotics and engineering?
I like to say I come from a “family of engineers.” I grew up in Mexico, and I remember being on the rooftop with my dad or in his shop, watching him—and later helping him—fix things.
My grandfather was also a big influence on me. He was obsessed with technology and started his own tooling company where everyone in our family worked at some time or another. He had a state-of-the-art facility and machinery. Just being around tools and machinery all the time is what initially sparked my interest in engineering.
When I was 14 my family moved to Michigan, where my father worked for a tooling company in the auto industry. Being around factory plants further deepened my interest in becoming an engineer. But it wasn’t until joining a robotics club in high school that I had my first real taste of engineering—and I was hooked. We were advised by engineers from Chrysler and had our own machine shop where we could tinker for hours, working on air cylinders, door motors, or whatever else we could get our hands on. Building our own machines and doing fabrication is what really cemented my desire to study engineering in college.
Q: What were you doing before building Canvas?
After getting my bachelor’s in mechanical engineering from MIT, I decided to stay at the university to pursue my Ph.D. as a graduate student. My work focused on centimeter-scale robotics and “no barcode” machines, which are cheap, low-energy robotics for one-time uses. After graduation, I worked at the MIT Lincoln Laboratory and later joined the team at Pneubotics, which became best known for our soft, inflatable robots. At Pneubotics, I also served as an advanced robotics engineer and later the director of engineering.
I met Kevin Albert, one of my co-founders and the CEO of Canvas, in Boston. As we worked together, we realized that our work in robotics could have a positive impact on the world outside the lab. The move from research idea to tangible business was a big transition, but it was an exciting jump to make.
Q: Why did you choose to focus the company on solving the challenges facing the construction industry?
Construction has historically been neglected by the robotics industry and has resisted pushes for automation. But it was clear that the times were beginning to catch up with construction—declining productivity, rising costs, an aging workforce, and dangerous conditions with increasing safety requirements are only some of the issues they face.
Even for us, it was not clear at first that construction was where we could make the biggest impact. Initially, the auto industry seemed like an obvious choice: It would have been easy to implement automation since everything in the automotive environment is highly controlled. But what motivated us was to bring productivity increases and new tools to industries that were most in need. So, we spent a lot of time thinking about the role that robots could play in less structured, more challenging environments. And as we explored, construction was the one area that just kept popping up.
With very little innovation in this space, we felt like robotics—specifically bringing our approach of instant calibration and compliance which enables robots that can efficiently operate in unstructured environments—could be used to meaningfully address the challenges facing the construction industry today.
Q: What problems were you trying to solve with your first product, the Canvas machine?
We first set out to tackle the issues with the work of drywall finishing, which represents one of the dirtiest, most congested and often most dangerous portions of construction. Studies have shown that drywall finishing has the highest proportion of work-related musculoskeletal injuries among such trades. It’s also often over budget and frequently behind schedule. What was really surprising to me was that most skilled tradesmen were still relying on the same set of tools that their grandfathers and great-great-grandfathers used in the past—in fact, they were relying on the same tools a homeowner might use.
Canvas is changing all this. We’re putting better and safer tools in the hands of skilled workers by creating a new class of robotics, while training and teaching union workers how to operate them. As a result of the introduction of our machinery, we were able to help improve productivity at the construction site, save time on drywalling, and reduce injuries for the workforce.
Q: In what ways do you think differently about your industry than others do?
What really sets us apart is our commitment to creating new and innovative opportunities for skilled workers. There was a lot of skepticism around automation and the introduction of robotics to the construction industry. The skepticism is centered around the fear of robots replacing human laborers. But at Canvas, we aren’t striving for full automation; we think about Canvas as a system, and the ways in which we can bring together what people are best at and where technology excels.
The Canvas system’s signature is enabling skilled union workers to operate robotics on-site. By improving safety conditions for skilled workers, our machine both creates longer careers for skilled workers and provides the opportunity for people who aren’t expert drywallers or roboticists to join the trade.
That’s a big reason why we sought the advice of and partnered with our local taper’s union very early on; we knew their skill and perspective was unmatched. And it’s turned out that we are motivated by the same vision and goal: To create beautiful spaces and rewarding careers. The union has been excited to partner with us because we make the trade more accessible to folks who have historically been excluded from it, and from the earliest days, we’ve been developing our machines with the feedback of these skilled workers.
Q: What challenge are you most proud of overcoming in your career?
I’m most proud of the team we’ve built at Canvas, which is composed of everyone from top roboticists to master tradespeople, all united in our mission to make this work better. It’s also exciting that one result of our work is that we are helping to make construction more accessible to minorities—and more sustainable for our future building needs.
Q: What is the most valuable lesson you’ve learned as the founder of your own company?
My co-founders and I had a lot of great ideas on our journey to build Canvas. But I’d say the most important lesson we’ve learned—and what we’d advise others to do, too—is to build for problems, not just innovation for innovation’s sake.
I’ve always seen engineering and robotics as fields that are rooted in helping to make people’s lives safer and easier. Although Canvas is fundamentally a robotics company, people are at the heart of everything we do. And we’ve integrated that people-centric mentality into our mission and into our products.
From the very beginning, we’ve built in partnership with the industry, seeking their advice and feedback, and looking to really understand their problems, because that’s the only way we can take robots out of the factory and bring them into the real world. It’s something that’s made a major difference for us, but I think is applicable to entrepreneurs everywhere.
Q: What would you say to young girls who want to pursue a career in robotics?
Go for it! I’m passionate about encouraging girls to pursue careers in STEM, especially robotics, and I think you’re never too young to start learning about the fields. Reach out to female engineers and share your passion or questions, you’ll find that there are a lot of people out there wanting to foster STEM, you just have to ask. Let your curiosity and creativity drive you一whether it’s joining the robotics team, taking that interesting science class, or tinkering in your own garage.